Récupération d’énergie lors de la production de céramiques
Dans le contexte énergétique mondial, il y a aujourd’hui des aspects à prendre particulièrement en compte, tels que le manque de ressources intérieures, la dépendance à l’approvisionnement en énergie provenant de l’étranger, les problèmes relatifs à la construction de nouvelles infrastructures, etc. Ces questions demeurent à ce jour sans réponse ni solution simple. En outre, le réchauffement climatique est une inquiétude de taille pour la majeure partie de la communauté scientifique et de la population mondiale, comme l’attestent le Protocole de Kyoto et la directive européenne qui en assure l’application en Europe. Le secteur de l’industrie céramique, depuis des années, prend des mesures pour réduire la consommation énergétique de ses machines. La preuve en est l’évolution de la consommation d’énergie dans le secteur céramique, ainsi qu’une comparaison entre l’Espagne et l’Italie des émissions spécifiques au secteur des carreaux.
Un échangeur de chaleur est un dispositif de récupération de la puissance thermique pour chauffer l’air ambiant. Une fois débarrassé de toute particule polluante (pour empêcher toute détérioration de la structure des machines), l’air est injecté dans le processus de cuisson, séchage et/ou pulvérisation, réduisant ainsi sensiblement la consommation de carburant. Ce dispositif semble permettre un amortissement rapide des investissements et pouvoir devenir rapidement une source de bénéfices fiable une fois amorti.
Le présent article examine en détail les caractéristiques techniques et économiques de la viabilité du dispositif dans le cadre de son intégration au processus céramique, qu’il s’agisse des carreaux ou de la céramique structurelle, au sein duquel il se sert de la chaleur résiduelle du processus de cuisson pour le processus de séchage et de pulvérisation. L’introduction de cette technologie constitue une étape importante dans l’économie d’énergie liée au gaz naturel et, par conséquent, la réduction des émissions de CO2.
Problèmes actuels liés à la récupération d’énergie provenant des gaz chauds
Les gaz provenant de la combustion du gaz naturel – en général et dans le cas sur lequel porte une partie de l’étude sur les moteurs de cogénération – du fait de leur débit et de leur température, sont réutilisés dans les séchoirs (à tunnel et à chambres) pour le séchage des tuiles. Cependant, l’utilisation de ces gaz entraîne les problèmes suivants au sein de l’usine :
PROBLÈMES D’ENTRETIEN
Les gaz sont introduits dans les séchoirs à tunnel et à chambres. Le problème réside principalement dans le séchoir à tunnel. Dans ces tunnels, des structures métalliques servent de chariots pour la manipulation et le déplacement des tuiles à l’intérieur des séchoirs. En raison de leur composition, les gaz d’échappement contiennent une forte proportion d’humidité ainsi qu’une quantité importante d’éléments corrosifs. Cela entraîne l’oxydation d’un grand nombre de chariots mobiles et d’éléments métalliques (mobiles ou fixes) restant en contact direct avec ceux-ci, entraînant d’importants coûts d’entretien pour la réparation et/ou le remplacement des éléments oxydés.
Par conséquent, on recherche des mesures correctives visant à éliminer le problème.
PROBLÈMES DE SÉCURITÉ ET DE SANTÉ DES OPÉRATEURS
Ceux-ci se rapportent principalement aux séchoirs à chambres. Les opérateurs chargés de la manipulation pour ce type de séchoir subissent des troubles légers dus à l’exposition aux gaz d’échappement utilisés dans ces machines. Il s’agit principalement d’irritations occulaires qui rendent difficile le travail des opérateurs.
L’exposition des opérateurs aux gaz d’échappement se produit principalement pour deux raisons :
– Les séchoirs à chambres fonctionnant sous pression, il est très possible que de petites fuites apparaissent et que l’environnement de travail des opérateurs soit pollué.
– Lors du vidage du séchoir et de l’ouverture des portes, du fait de la pression à l’intérieur de la machine, une certaine quantité de gaz d’échappement est libérée dans l’usine, affectant non seulement les opérateurs qui vident les chambres mais aussi les travailleurs se trouvant à proximité du séchoir à chambres.
Ces expositions se traduisent tout d’abord par des irritations occulaires pour les opérateurs. Mais une exposition prolongée à ces gaz irritants est susceptible de causer des lésions importantes au niveau des muqueuses des voies respiratoires. L’ampleur des lésions touchant les voies respiratoires est fonction de l’intensité (concentration des gaz dans l’environnement) et de la durée de l’exposition.
PROBLÈMES DE PERTE DE CHARGE
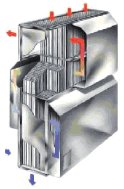
La distribution des gaz d’échappement depuis les moteurs de cogénération vers les diverses installations exploitant cette énergie (chaudières à vapeur et séchoirs) entraîne une certaine perte de charge. Cette perte de charge détermine la pression des gaz d’échappement à la sortie des moteurs de cogénération. À l’heure actuelle, la perte de charge qui se produit entre la sortie des moteurs de cogénération et la chambre de mélange est de 50 mbars. D’autre part, nous savons que les moteurs en fonctionnement sont seulement capables de supporter une pression de 65 mbars à la sortie. Si la perte de charge venait à dépasser 65 mbars, les moteurs s’arrêteraient. Par conséquent, les ajustements doivent prendre en compte la perte de charge. La mise en oeuvre de tout dispositif correctif des deux problèmes soulevés ci-dessus (l’entretien, ainsi que la sécurité et la santé) peut agir sur les valeurs de la perte de charge et, ainsi, conduire à l’arrêt des moteurs.
SOLUTION AUX PROBLÈMES SOULEVÉS
Face à cette situation, et après avoir réalisé une étude approfondie des différentes possibilités, on estime que la mise en oeuvre d’un échangeur de chaleur gaz/air pour utiliser l’air ambiant chaud à la place des gaz d’échappement élimine les problèmes d’entretien et de sécurité des opérateurs. Cet objectif est atteint sans que le fonctionnement actuel des séchoirs ou leur rendement ne soient affectés.
Échangeur de chaleur, description des composants du dispositif
Les composants du dispositif sont les suivants :
TYPE D’ÉCHANGEUR DE CHALEUR
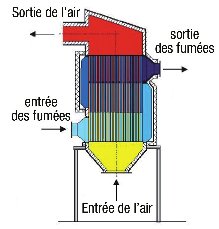
Le corps de l’échangeur est formé d’une batterie de tubes en acier sur une structure interne (coque). Il s’agit d’un équipement préchauffeur d’air de type coque et tube, comprenant un ensemble de tubes verticaux à travers lesquels circule l’air propre et une enveloppe extérieure autour de laquelle circulent les gaz de combustion. L’échangeur de chaleur est de forme rectangulaire, comme sur la figure 1.
Afin de répondre aux spécifications fixées pour le processus, qui exigent une température de sortie pour l’air propre d’environ 150º C, une surface d’échange de chaleur de 536m2 est nécessaire. Ce type d’échangeur de chaleur est utilisé dans de nombreuses installations industrielles, notamment les raffineries de pétrole, les centrales électriques et les installations de climatisation et de réfrigération.
Comme le montre la figure 2, les gaz de combustion passent à travers le faisceau de tubes à l’intérieur de la coque et traversent les tubes contenant l’air propre à trois reprises. Leur trajectoire est déterminée par deux « chicanes » ou plaques de séparation de flux et par la coque extérieure pour le changement de sens des gaz.
La vitesse des gaz de combustion et de l’air est adaptée pour éviter les vibrations et l’érosion des tubes, ainsi que le dépôt de cendre et de suie. L’unité est isolée pour éviter les pertes de chaleur et améliorer la sécurité des travailleurs.
TUBES DE L’ÉCHANGEUR
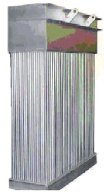
Les tubes sont alignés et supportés par deux plaques tubulairesau niveau des extrémités d’entrée et de sortie. Ces extrémités sont soudées aux plaques tubulaires, assurant la stagnation des gaz et la rigidité mécanique de l’équipement.
Comme nous l’avons vu, l’échangeur est constitué d’une batterie de tubes en acier au carbone disposés à la verticale, comme le montre la figure 3.
RÉGLAGE DU DISPOSITIF
Pour fonctionner correctement, un échangeur de gaz/air nécessite
l’installation de deux boucles de commande qui régissent :
– Le fonctionnement du ventilateur d’aspiration dans le conduit du flux de gaz d’échappement
– Le fonctionnement du ventilateur d’insufflation d’air ambiant à l’intérieur de l’échangeur.
Le réglage se fait de la manière suivante :
– Réglage du ventilateur d’aspiration : le réglage se fait au moyen d’un régulateur PID qui contrôle un variateur de fréquence en fonction des signaux fournis par un capteur de pression placé dans le conduit des gaz d’échappement, avant l’entrée de l’échangeur. Le variateur de fréquence agit sur le moteur du ventilateur d’aspiration (sortie), le déclenchant ou l’éteignant selon les besoins. Le régulateur PID compare ces signaux de pression avec une pression négative constante pré-établie. Si le signal de pression provenant du capteur est différent de la pression pré-établie, le régulateur PID active le ventilateur d’insufflation jusqu’à ce que la pression mesurée par le capteur atteigne le niveau pré-établi.
– Réglage du ventilateur d’insufflation : le réglage du ventilateur d’insufflation se fait selon les mêmes paramètres que le cas précédent, la seule différence étant que le ventilateur est placé en tête plutôt qu’en queue et que le capteur de mesure de la pression est placé dans le conduit d’air extérieur à la sortie de l’échangeur. Dans ce cas, la pression constante pré-établie est positive. La température de l’air chaud propre à la sortie peut être ajustée à l’aide de ce ventilateur. Le schéma des boucles de commande est présenté dans la figure 4.
VENTILATEUR D’ASPIRATION
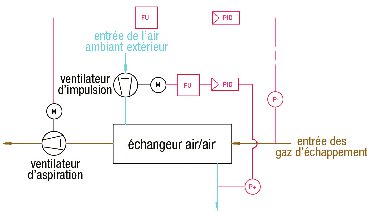
Le ventilateur d’aspiration est installé à la suite de l’échangeur gaz/air. En fonctionnement, il fournit un débit de 45800 kg/h de gaz d’échappement générant une dépression égale à la perte de charge due à l’installation de l’échangeur luimême au milieu de la canalisation. Cette perte de charge est d’environ 70 mm.c.e. Le ventilateur selectionné a été conçu pour fonctionner correctement avec des gaz d’échappement à haute température.
Ainsi, en ce qui concerne la perte de charge, le dispositif est invisible du fait que sa mise en oeuvre n’augmente pas la perte de charge dans la canalisation et n’augmente donc pas la pression à la sortie des moteurs. Le rôle de ce ventilateur est de faire en sorte que l’installation de l’échangeur de chaleur ne nuise pas au bon fonctionnement des moteurs.
En outre, ce ventilateur peut être surdimensionné afin de produire une dépression supérieure à la perte de charge causée par l’échangeur de chaleur. Ainsi, le ventilateur d’aspiration absorberait la perte de charge de la canalisation qui est, à l’heure actuelle, supportée par la sortie des moteurs de cogénération. Ce type de dispositif assurerait davantage le fonctionnement des moteurs de cogénération du fait qu’il peut absorber d’éventuels pics de perte de charge lors des opérations d’ouverture/de fermeture des canalisations.
VENTILATEUR D’INSUFFLATION
Le ventilateur d’insufflation doit être installé sur l’autre ligne de l’échangeur gaz/air. Ce ventilateur insuffle un débit de 52 000 kg/h d’air extérieur à température ambiante et à une pression donnée, suffisante pour surmonter les pertes de charge dues au passage dans l’échangeur et celles dues à la canalisation allant de l’échangeur à la chambre de mélange. La perte de charge à l’intérieur de l’échangeur pour les gaz d’échappement est mesurée à 80 mm.c.e.
À ce stade, il convient de noter que les pertes de charge dues à la canalisation allant de l’échangeur à l’entrée de la chambre de mélange n’auront pas à être supportées par la pression de sortie des moteurs comme c’est le cas actuellement, mais seront compensées par le ventilateur d’insufflation. Cela signifie que la pression à la sortie des moteurs de cogénération sera moindre, ce qui agira positivement sur leur fonctionnement. Un ventilateur de type particulier n’est pas nécessaire puisqu’il travaille avec de l’air extérieur à température ambiante.
MISE EN SERVICE ET ENTRETIEN
Avant la mise en service, il faut veiller à ce que les flux de gaz d’échappement et d’air extérieur puissent circuler librement dans les tubes et la coque. Si on installe des amortisseurs, il faut vérifier qu’ils puissent se mouvoir librement et qu’ils soient correctement ajustés.En outre, il faut vérifier que l’ensemble est correctement installé et s’assurer que les limites d’application (température, différence de pression, matériel, etc.) ne sont pas dépassées.
Pour l’entretien de l’échangeur une fois installé, seules des inspections visuelles sont nécessaires. Si des amortisseurs sont installés, il faut vérifier leur mobilité. Initialement, les inspections doivent être effectuées tous les mois. Après trois mois, les contrôles doivent se faire tous les douze mois.
Pour faciliter son assemblage et son montage, l’échangeur dispose de quelques pattes de levage et appuis latéraux supportant la structure aux endroits prévus.
L’équipement est fourni avec des brides d’entrée et de sortie pour l’interconnexion avec les conduits d’air et de gaz. Tous les joints sont vissés afin de pouvoir les monter/démonter autant que nécessaire.
Application industrielle, spécifications et restrictions
Cet échangeur a été installé dans une usine de tuiles céramique, comme expliqué ci-dessous. Au départ, la demande consistait en la conception et la mise en service d’un échangeur de chaleur air/air pour récupérer l’énergie thermique des gaz d’échappement à 270 °C provenant de moteurs de combustion. La chaleur est transférée de ce flux de gaz d’échappement à un flux distinct d’air propre provenant de l’extérieur de l’usine. L’installation correspond aux spécifications et restrictions du client se rapportant au produit à fabriquer comme au lieu d’implantation de l’installation.
SPÉCIFICATIONS
Les spécifications relatives au dispositif peuvent être classées en plusieurs catégories :
Spécifications d’exploitation du client :
a) Maintenir le mode de travail actuel. Le client souhaite conserver le mode de travail en place à l’usine. À l’heure actuelle, le flux des gaz d’échappement alimente deux installations : une partie du flux est dirigée vers une chambre de mélange où se rencontrent différents flux provenant d’autres processus, et l’autre partie du flux alimente un séchoir à chambres.
Ces gaz d’échappement provoquent des irritations chez les opérateurs postés dans la zone des séchoirs à chambres ; il est donc nécessaire que l’échangeur puisse fournir de l’air chaud propre pour maintenir le fonctionnement des séchoirs sans causer de problèmes aux travailleurs.
Ainsi, ces spécifications impliquent que :
– Le flux d’air propre/d’air chaud provenant de l’échangeur de chaleur doit être égal au flux de gaz d’échappement actuel.
– La température de l’air propre doit être supérieure à 150ºC.
b) Provoquer le moins de perte de charge possible. Les moteurs de production d’électricité ne peuvent supporter qu’une certaine pression de sortie (65 mbar maximum). Toute modification apportée doit permettre aux moteurs de continuer à fonctionner et faire en sorte que la pression à la sortie de ceuxci soit inférieure à 65 mbar.
c) Éliminer les problèmes découlant de l’utilisation des gaz d’échappement. Réutiliser l’énergie des gaz d’échappement dans les séchoirs (à chambres et à tunnel) cause deux types de problèmes (entretien et sécurité) qui sont abordés ci-dessous.
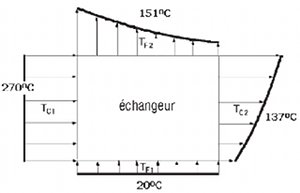
Spécifications relatives aux flux :
a) Flux à employer. L’échangeur est conçu pour permettre l’échange de chaleur entre les flux de l’usine, soit :
– L’air propre provenant de l’extérieur de l’usine.
– Les gaz d’échappement provenant du générateur d’électricité appartenant à l’entreprise, qui a recours à quatre moteurs à gaz naturel.
b) Propriétés des flux. Les gaz d’échappement disposent des propriétés suivantes :
– Débit : 45 800 kg/h.
– Température d’entrée : 270 ºC.
Air propre provenant de l’atmosphère :
– Débit : 52 000 kg/h.
– Température d’entrée : variable selon les saisons.
Conception du dispositif
Lors de la conception de l’échangeur, on a retenu comme pire scénario une quantité d’air à chauffer de 52 000 kg/h. Avec une température ambiante de 20º C, l’échangeur à coque et à tubes doit faire passer 52 000 kg/h d’air propre de 20ºC à 151ºC. Ainsi, un débit de 45800 kg/h de gaz d’échappement entrant dans l’échangeur à 270º C doit être refroidi pour atteindre 137 ºC. Grâce à l’étanchéité de la circulation des flux dans l’échangeur, les deux flux (air et gaz d’échappement) ne sont pas en contact direct et ne se mélangent donc pas. La transmission de la chaleur (refroidissement de l’un, chauffage de l’autre) se fait par les tubes. Le diagramme des températures est illustré dans la figure 5.
Exemple de récupération de la chaleur d’un four de cuisson de carreaux pour deux séchoirs
DONNÉES TECHNIQUES ET ÉCONOMIQUES
• Machine depuis laquelle l’énergie thermique est récupérée :
four à porcelaine (Temp : 1 200 ºC)
• Machines ayant recours à l’énergie thermique : séchoir à la
sortie de la presse
Nombre de fours : 1
• Production journalière : 7 500 m2/jour.
• Format : 45 x 45 cm.
• Température cheminée : 200ºC.
• Débit cheminée : 16 500 Nm3/h.
Nombre de séchoirs : 2
• Température de travail : 140ºC.
• Débit cheminée : 21 284 Nm3/h – 30 000 kg/h
• Heures de mise en service : 8 000 heures/an (par séchoir).
• Consommation de gaz naturel : 80 Nm3/h (par séchoir).
• Consommation annuelle de gaz naturel : 640.000 Nm3/an (par séchoir).
Données de calcul
Coût gaz naturel 0,34 €/Nm3
Coût KWh électricité 0,12 €/KWh
Heures de mise en service par an 8 300,00 heures
Énergie thermique
Débit d’air chauffé 18 146,00 kg/h
Température à l’entrée 20,00 ºC
Température à la sortie 170,00 ºC
Économie d’énergie 656 004,15 Nm3/an
Électricité
Puissance des moteurs de ventilateur 36,01 KW
Consommation annuelle d’électricité 298 897,86 KWh/an
Économie brute d’énergie (GN) 223 041,41 €/an
Dépenses d’électricité 35 867,74 €/an
Coût annuel O&E 6 072,83 €/an
Total des économies d’énergie 181 100,83 €/an
Exemple de récupération de la chaleur d’un four de cuisson de carreaux pour un atomiseur
DONNÉES TECHNIQUES ET ÉCONOMIQUES
• Machines depuis lesquelles l’énergie thermique est récupérée : 4 fours de cuisson des carreaux céramique
• Machines ayant recours à l’énergie thermique : 1 atomiseur.
• Matériaux cuits dans le four : grès pâte blanche et porcelaine.
• Température de cuisson : 1 120 ºC – 1 200 ºC.
Nombre de fours : 4
• Température de travail : 200ºC (chacun).
• Débit cheminée : 52 000 Nm3/h (les 4 fours).
• Production journalière : 7 000 m2/jour (par four).
Nombre d’atomiseurs : 1
• Capacité d’évaporation de l’eau : 6 600 l/h.
• Production d’argile : 16 500 kg/h.
• Débit d’air à l’entrée : 41 500 Nm3/h.
• Température de travail : 520 – 600 ºC.
• Heures de mise en service : 8 300 h/an.
• Consommation de gaz naturel : 616 Nm3/heure.
• Consommation de GN annuelle : 5 112 800 Nm3/an.
Données de calcul
Coût gaz naturel 0,34 €/Nm3
Coût KWh électricité 0,12 €/KWh
Heures de mise en service par an 8 300,00 h
Énergie thermique
Débit d’air chauffé 66 368,00 kg/h
Température à l’entrée 20,00 ºC
Température à la sortie 170,00 ºC
Volume de gaz économisé 2 399 299,20 Nm3
Électricité
Puissance des moteurs de ventilateur 104,00 KW
Consommation annuelle d’électricité 407 613,00 KWh/an
Économie brute d’énergie (GN) 815 761,73 €/an
Dépenses d’électricité 103 584,00 €/an
Coût annuel O&E 7 894,68 €/an
Total des économies d’énergie 704 283,04 €/an
Conclusions sur le dispositif
L’installation d’un échangeur de chaleur gaz/air, dont traite le présent article, présente les propriétés suivantes :
– Maintien des conditions de travail actuelles, étant donné qu’il s’agit d’un débit de 45 800 kg/h à 270ºC et que l’échangeur gaz/air obtient un débit de 52 000 kg/h à une température de 151ºC, c’est-à-dire supérieure aux 150ºC nécessaires au fonctionnement des séchoirs.
– Élimination à 100 % de l’utilisation des gaz émis dans les séchoirs, remplacée par l’utilisation d’air chaud, ce qui évite les problèmes d’entretien comme de sécurité et de santé des opérateurs.
– La stabilité des matériaux utilisés dans l’échangeur de chaleur garantit qu’il ne fera pas l’objet d’un processus de corrosion et d’oxydation, que subissent les composants métalliques (fixes et mobiles) des séchoirs.
– L’installation d’un échangeur de chaleur ne constitue pas un risque pour le fonctionnement du moteur puisqu’il aura seulement un effet positif sur la pression à la sortie des gaz d’échappement en la diminuant, et aidera ainsi à maintenir en bon état les moteurs de cogénération. On considère ainsi que l’échangeur viendra à l’appui de leur fonctionnement.
– Le coût de mise en oeuvre et d’entretien est très bas car il n’y a pratiquement pas de composants.
– Viabilité économique pour nos commerces et entreprises puisque l’équation investissement-rentabilité-économies est satisfaite pour toutes et chacune des variables.
– Conséquences environnementales. La réutilisation de l’énergie permet d’économiser une grande quantité de celle-ci, ce qui se traduit par une réduction des émissions de gaz à effet de serre et de CO2.
j’ai des problème dans mon usine de céramique je fais des carreau en terre cuite a Tunis merci.
HELLO
I WANT OPEN NEW CIRAMIC AND CARLLAGE FACRTORY IN ALGERIA
CAN YOU SEND TO ME YOUR MACHINES CATALOGUE WITH PRICES AND PLAN OF WHAT I NEED .
I AM WIATING FOR YOUR REPLAY
THANKS
Bonjour,
si vous avez des problemes ou des questions (Chemie mineralogie,Reologie,céramique technique..) vous pouvez me contacter. je peux vous aider.
Nacef remouqui
ceramique institut
Höhr Grenzhausen
nacef@hotmail.de
Monsieur, j’ai besoin d’uen réponse sur cette question:
comment vous expliquez que l’air chaud provenant de la cogénération à la sortie de la chambre de mélange ne soit pas totalement aspiré dans les ventilateurs d’introduction du séchoir à balancelles des briques, une partie de l’air chaud passe dans le sens contraire du séchoir et détruit les composantes électroniques du chargeur des briques installé à avant le séchoir. sachant que les ventilateurs séchoirs sont dimensionnés pour absorber le flux d’air chaud provenant de la turbine après avoir être dilué avec de l’air frais dans la chambre de mélange.
le problème disparait en arrêtant la cogénération et utilisant les générateurs d’air chaud du séchoir.
merci
Nous sommes une société qui travaille sur l efficience énergétique et la récuperation de chaleure dans les usines céramique et briqueteries
j’ai une usie de céramique utilisant des sechoirs et en hiver je veux proceder à la récuperation de la chaleur dégagée par ces sechoirs.
j’ai une usine de céramique utilisant des sechoirs et en hiver je veux proceder à la récuperation de la chaleur dégagée par ces sechoirs.
salut monsieur Nacef Remouqui. Je suis un étudiant en génie des procédés et matériaux céramiques .je voudrais savoir comment procéder pour faire la conception d’un four à rouleaux pour les carreaux céramiques,et merci d’avance pour la richesse des infos exposer sur votre site.
HELLO
I WANT OPEN NEW CIRAMIC AND CARLLAGE FACRTORY IN ALGERIA
CAN YOU SEND TO ME YOUR MACHINES CATALOGUE WITH PRICES AND PLAN OF WHAT I NEED .
I AM WIATING FOR YOUR REPLAY
THANK
amineelhoma@hotmail.com