Séchage de l’argile par cogénération de carreaux céramiques
Dans cet article, sont examinées deux options (turbogénérateur et moteur) utilisant du gaz naturel comme application de la cogénération thermoélectrique par rapport à un chauffe-air classique dans le cadre d’un processus de séchage artificiel de la matière première pour la production à sec de carreaux céramique.
Étant donné le processus de séchage et la manière dont il agit sur les matières premières, les études et essais en laboratoire menés sur les échantillons d’argile se sont concentrés sur la recherche de la température la plus adéquate pour les gaz de séchage et du type de séchoir à utiliser afin de conserver les meilleures propriétés de l’argile après séchage.
Prenant en compte quelques exemples d’application de la cogénération dans l’industrie du secteur céramique au Brésil, l’étude a démontré la viabilité des opportunités de cogénération comme moyen efficace d’utiliser le gaz naturel en tant que complément de l’hydroélectricité pour répondre à la croissance de la demande d’énergie électrique dans le pays, par opposition aux installations électriques centrales.
Ces deux aspects nécessitent une vision novatrice des installations industrielles du cluster céramique le plus important des Amériques, dont la production atteint 300 millions m2 par an.
Au Brésil, plus de 80 % de la capacité d’énergie électrique déjà installée dans le pays provient de l’énergie hydraulique. Ces dernières années, le processus d’augmentation de la capacité de production et de réduction de la dépendance du pays à l’énergie hydraulique a commencé avec l’introduction d’enchères en ligne pour des offres de nouvelles capacités à un horizon allant de trois à cinq ans, excluant de fait tout nouveau projet d’énergie hydraulique.
Une technologie de cogénération thermoélectrique – produisant à la fois de l’électricité et de la chaleur – est l’un des moyens les plus simples d’utiliser le carburant primaire de manière efficiente et de réduire les émissions de CO2. Parce que la fourniture de chaleur sur de longues distances est complexe, la cogénération se traduit souvent par des solutions énergétiques réparties, mais on peut également exploiter de petites installations réparties sur l’ensemble d’une zone de grande taille pour fournir de l’énergie aux heures de pointe, stabilisant ainsi le réseau d’approvisionnement.
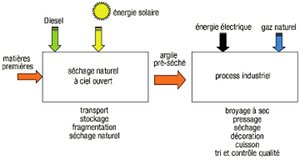
D’après Berg et Nogueira (1996), la viabilité de la cogénération au Brésil est quelque peu variable, en fonction des législations particulières et des coûts relatifs de l’énergie, ce qui constitue une entrave à l’expansion voulue. Dans le passé, il y a eu quelques difficultés à garantir l’approvisionnement en gaz naturel ; mais cette situation est en train d’évoluer rapidement avec la mise en oeuvre de mécanismes fondés sur les politiques énergétiques garantissant l’approvisionnement en gaz naturel des installations industrielles.
Toutefois, jusqu’à présent, il n’y a eu que peu d’applications de la cogénération au Brésil. La dernière d’entre elles est une installation basée sur des turbines de gaz naturel (ISO 4 500 kWe) au sein de l’entreprise PAMESA. L’installation industrielle se situe dans la région Nord, dans la ville de Cabo de Santo Agostinho proche de la région métropolitaine de Recife. Il s’agit d’une application classique du schéma de cogénération à atomiseur, exportant une partie de l’énergie produite vers le réseau d’approvisionnement.
Les installations industrielles du secteur céramique au Brésil
Malgré la crise économique internationale de 2008, la production de carreaux en céramique au Brésil a atteint le chiffre de 713 millions de m2, faisant du pays le deuxième plus grand producteur au niveau international. Pour 2009, la production est similaire, avec une croissance estimée à plus de 5 % en raison de l’expansion de la demande intérieure. Le processus de production est de deux types : sec ou humide, en fonction de la méthode de broyage des matières premières.
Le pôle de fabrication céramique de Santa Gertrudes, situé dans l’État de São Paulo, au sud-est du Brésil, produit plus de 300 millions de m2 de carreaux par an dans environ 40 unités de fabrication.
Les principales caractéristiques des carreaux fabriqués à Santa Gertrudes sont celles du processus sec : le support céramique a une couleur rougeâtre, une absorption de l’eau comprise entre 6 % et 10 % (type BIIb) et une surface émaillée. La fabrication par processus sec se fait à partir d’une seule matière première (argile), utilisée dans la composition du support.
Cette matière provient des rochesargileuses du bassin de la rivière Paraná, un grand bassin sédimentaire intracratonique du Phanérozoïque qui s’étend sur 1100000 km2 au sud du Brésil, et 100000 km2 en Uruguay, au Paraguay et en Argentine.
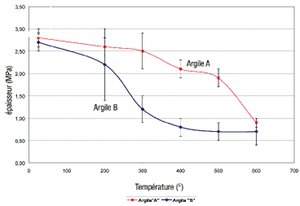
Dans la région du pôle de Santa Gertrudes, les roches argileuses utilisées comme matière première dans la fabrication de substrats pour les carreaux se trouvent dans la formation du Permien de Corumbataí.
Il s’agit d’une couche superficielle allant jusqu’à environ 130 m d’épaisseur de sédiments marins rougeâtres contenant de l’argilite, du schiste, de la siltite et du grès fin. Les principaux minéraux présents dans ces roches argileuses sont l’illite et de petites quantités d’argile smectique et de kaolinite, ainsi que du quartz, du feldspath, de l’hématite et des hydroxydes de fer. Les principaux oxydes présents et leurs compositions approximatives sont : SiO2 (67 %), Al2O3 (15 %), Fe2O3 (5 %), K2O (3-4 %), Na2O (0.5 %) et CaO (0.5 %).
L’exploitation minière se fait par la méthode traditionnelle à ciel ouvert, qui implique les étapes typiques de dégagement de la végétation (champs de cannes à sucre) et de déracinement, suivi d’un dynamitage ou d’un raclage (selon la dureté de la roche), en utilisant des bancs simples ou multiples. Le minerai, sous forme de pierres et de cailloux, est chargé sur des camions et transporté en tant que production brute vers des stocks d’altération à l’air libre ou vers un concasseur primaire, puis vers des terrasses extérieures pour mixage, réduction de la taille des grains, homogénéisation et séchage au soleil.
Cependant, le travail de séchage à l’extérieur génère une grande quantité de poussière, qui part dans l’atmosphère et dans le réseau d’égoûts, ce qui nuit à la qualité de l’air et de l’eau. Pour réduire cette pollution, l’agence environnementale locale a mis en place toute une série de restrictions relatives à cette méthode de séchage.
Dans une recherche d’alternatives techniques et environnementales, l’étude menée et présentée ici traite d’une application de cogénération pour le séchage de l’argile en intérieur plutôt qu’en extérieur. Cette application n’est pas habituelle, et ses résultats font toujours l’objet d’analyses.
Les principaux objectifs de cette étude étaient de :
• Rechercher en laboratoire les limites de température pour le processus de séchage artificiel afin de sauvegarder les propriétés de l’argile, en particulier celles liées à la plasticité et à la résistance mécanique du brut ;
• À partir des travaux menés en laboratoire, concevoir un séchoir classique, doublé d’options de cogénération pour une installation in dus trielle céramique typique en prenant en compte les aspects locaux et les coûts énergétiques associés;
• Estimer les coûts qu’impliquent ce nouveau processus de séchage de l’argile par rapport à cette méthode ainsi que ses effets sur l’impact environnemental ;
• Fournir une base pour l’évaluation gouvernementale, comme par exemple les avantages et les désavantages de la cogénération d’énergie électrique in situ, par rapport à la production hors site à l’aide de gaz naturel.
Consommation d’énergie et émissions du séchage naturel
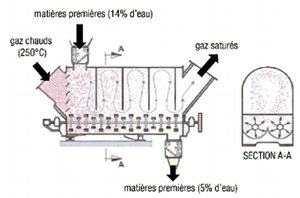
Le processus actuel de séchage de l’argile à Santa Gertrudes est montré de manière simplifiée dans le diagramme des flux de la figure 1. Malgré l’utilisation du soleil comme principale source d’énergie, on utilise toujours beaucoup de diesel pour les travaux sur les terrasses ouvertes et pour le transport. Les mouvements intensifs de matière première dans ces opérations impliquent des coûts élevés, ainsi qu’une pollution de l’air et de l’eau à proximité des sites concernés.
Les options de séchage forcé
Afin d’essayer de remplacer le séchage naturel, certaines installations ont adopté un système de séchage classique. Dans les deux cas analysés, on a utilisé deux types de séchoirs rotatifs, dans lesquels on introduit l’agent de séchage à une température comprise entre 300 ºC et 400 ºC. Dans les deux cas, on a observé quelques modifications dans les propriétés de l’argile. La solution adoptée par les producteurs a donc été de limiter à 50 % la quantité d’argile séchée de manière artificielle dans la composition totale de l’argile.
Pour la présente étude, on a procédé à de nombreux essais en laboratoire afin d’étudier le comportement de l’argile sous différentes températures de séchage afin de déterminer la température maximale permettant d’éviter les pertes importantes de plasticité. Ainsi, la figure 2 montre une diminution de la résistance mécanique du support céramique séché à des températures plus élevées pour deux échantillons d’argile de la région de Santa Gertrudes.
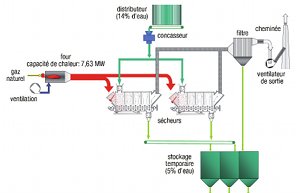
La valeur de résistance a été l’un des paramètres les plus importants lors de l’évaluation de la meilleure température de séchage. Il a été établi qu’une température légèrement inférieure à 250ºC peut fournir une certaine efficacité au processus et préserver les caractéristiques particulières de l’argile dans l’étape de pressage à sec. Compte tenu de ces résultats, le processus de séchage doit se faire à une température basse avec un temps de séjour court et, dans ce cadre, l’utilisation d’un séchoir de type chambre de « séchage rapide » (figure 3) devrait fournir de meilleurs résultats que les séchoirs rotatifs de type classique.
Pour la présente étude, on a utilisé deux unités de « séchage rapide » pour réaliser l’installation typique, par exemple, pour une production de 1,65 millions m2 de carreaux par mois.
Dispositifs de séchage classiques
Afin d’étudier une application pour un cas typique, on a pris en compte les paramètres suivants afin de préciser la capacité de traitement à l’usine de pré-séchage : 59 m2 de carreaux/t d’argile ; 550,000 m2/mois ; production d’argile sèche : 31,25 t/h (capacité nominale : 40 t/h).
Malgré la présence de différents types d’argile dans la région, on a adopté les valeurs suivantes afin de réaliser le meilleur calcul possible : teneur en eau de l’argile naturelle : 15%; eau dans l’argile sèche : 5 %, ce qui se traduit par 4 000 kg/h de débit d’eau évaporée. En supposant un rendement thermodynamique du séchage de 81 % et une consommation spécifique d’énergie de : 1000 à 1200 Kcal/kg d’eau évaporée, ce qui est typique pour les séchoirs avec une température d’air de 250º C, qui se traduit par une capacité calorifique maximum de 4,8 Gcal/h (5,58 MW), et un débit de 63 000 kg/h des gaz de séchage.
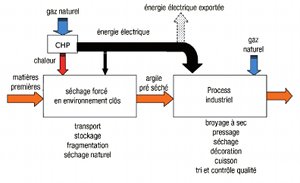
On a pris comme référence pour les comparaisons un dispositif de séchage classique utilisant un fourneau (chambre de combustion) produisant des gaz chauds pour la cuisson directe par gaz naturel, comme l’illustre la figure 4. Dans ce cas, la capacité nominale du fourneau est de 7,63 MW.
Schémas d’application de la cogénération
Dans le diagramme des flux de la figure 5, on considère que la cogénération répond aux demandes d’énergie électrique et thermique pour le séchage forcé de l’argile en intérieur ; une partie de l’énergie électrique sera exportée vers des installations industrielles, situées à proximité dans certains cas, ou ira dans un réseau d’approvisionnement en électricité. Suivant l’option (moteurs ou turbines), l’excédent d’énergie devra être exporté vers le réseau d’alimentation externe. Dans la figure 6, le dispositif se compose de trois moteurs à pistons avec une puissance nominale (de 2 MWe chacun) suffisante pour alimenter en gaz chaud les deux séchoirs. Les gaz d’échappement doivent être dilués avec de l’air frais pour maintenir la température de séchage à 250 ºC à l’entrée des séchoirs.
Dans la figure 7, le dispositif se compose d’un groupe turbogénérateur (compresseur d’air et turbine), avec une puissance nominale de 3 MWe, suffisante pour alimenter en gaz chauds deux séchoirs. Les gaz d’échappement doivent également être di-lués avec de l’air frais pour maintenir la température de séchage
spécifiée.
Analyse comparative des dispositifs
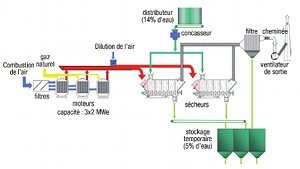
L’analyse suivante porte sur les trois options et tient compte du rapport chaleur-puissance électrique, ainsi que des paramètres économiques relatifs aux investissements. Pour obtenir la même énergie thermique, la puissance installée doit être assez différente du fait des différences au niveau du rapport chaleur/travail qui existe entre les deux options de cogénération. Ces chiffres sont estimés pour une installation typique et pour 1 650 000 m2 par mois (voir tableaux 1 et 2).
L’impact de la cogénération dans différents scénarios
De nos jours, il y a certaines limitations dans les systèmes de distribution d’électricité aux alentours de Santa Gertrudes. On s’attend à ce que la croissance économique fasse augmenter rapidement le marché intérieur des carreaux, ce qui exercera une pression sur les ressources en gaz naturel. Cependant, on s’attend également à une augmentation importante de la production de gaz à proximité de la zone côtière. En tenant compte de la nécessité de compléter la production d’énergie basée sur la production hydroélectrique à l’aide du gaz naturel pour répondre à la demande d’énergie, il importe de prendre en compte les applications de cogénération.
En se basant sur les seuls chiffres de Santa Gertrudes et une augmentation de la production estimée à 378 millions m2 de carreaux par an, quelques valeurs se rapportant au gaz naturel et à la consommation d’énergie électrique sont présentées dans les tableaux 3 et 4, qui couvrent des situations différentes : présent (séchage naturel), fourneau (séchage forcé classique) et les deux options de cogénération (moteur et turbine). Pour l’option moteur, la valeur négative représente la possibilité d’exporter vers le réseau d’alimentation externe de l’État de São Paulo. Les options turbine représentent une réduction de 63 % de la demande d’énergie électrique du réseau d’approvisionnement.
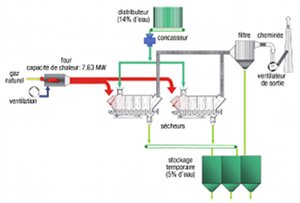
Le tableau 4 montre la consommation totale de gaz naturel dans l’État de São Paulo en tenant compte des trois options pour répondre à la demande d’énergie provenant des installations industrielles du pôle de Santa Gertrudes. Pour estimer la consommation de gaz naturel dans les installations de production d’énergie électrique centrales, trois variantes sont examinées : l’énergie électrique produite dans une centrale thermoélectrique située à Americana, très proche de Santa Gertrudes (voir la figure 1), alimentée par du fioul lourd (rendement 21 %). Le deuxième scénario se rapporte à une reconversion de la même installation, alimentée au gaz naturel (rendement = 35%). Le troisième se rapporte à la demande d’électricité fournie pour une installation thermoélectrique centrale située à Sao Paulo, alimentée au gaz naturel (rendement = 55%), à 180 km de Santa Gertrudes (voir figure 1). Tenant compte du facteur de rendement maximal pour la production centrale, l’utilisation de l’énergie locale produite au moyen de moteurs dans le cadre de l’option de cogénération représente une économie de 126.466 Nm3/jour (8,6 %) par rapport à l’option fourneau classique.
Conclusions
Le pôle céramique de Santa Gertrudes, dans l’État de Sao Paulo au Brésil, produit plus de 300 millions de m2 par an de différents types de carreaux, 100 % à base de pâte céramique en argile. L’argile est séchée au moyen d’un processus naturel, à l’aide du soleil, mais cela entraîne des problèmes environnementaux en raison de l’émission de particules très fines dans l’atmosphère et dans l’eau, en plus des coûts relatifs aux équipements et au combustible. Cette étude a évalué quelques paramètres techniques et économiques pour introduire des méthodes de séchage artificiel, certains étant des processus novateurs visant à réduire l’humidité naturelle de l’argile (environ 15 % en poids) à 5 %, pour atteindre les conditions souhaitables pour le broyage à sec. La préparation de la poudre par voie sèche est une solution typique et peu coûteuse pour les carreaux produits à Santa Gertrudes.
Parmi les principales conclusions, on peut citer :
• qu’il est possible de remplacer le dispositif actuel de séchage par un dispositif artificiel, mais certaines précautions sont nécessaires, telles que : la température de l’agent de séchage ne doit pas excéder 250° C et un cycle de séchage court est recommandé ;
• que certaines options combinant les processus et les équipements sont réalisables d’un point de vue économique et technique, mais la cogénération présente des avantages supplémentaires, surtout les dispositifs utilisant le moteur.
• en ce qui concerne la consommation totale d’énergie, la production d’énergie électrique d’une installation au gaz naturel devrait présenter plus d’avantages dans la cogénération locale, comme dans cette étude pour le séchage de l’argile, qu’une installation thermoélectrique centralisée
Je pense que c’est un bon travail vous faites mais comment acquerir toute cette technologie
je suis togolais titulaire de la licence en géologie je suis intéressée par cette méthode de fabrication des carreaux j’aimerais en faire carrière dans mon pays car il y a des argiles du bassin côtier qui recouvre les calcaire
J’ai cette technologie.
On la fais chez nous et moi je la vend.
pedro.rodrigues@saautomation.eu
Salutations.
j’aime cette techno, c’est qui le fournisseur de ce cogénération, pourriez vous me donner ses coordonnés.
merci
Je veux venir apprendre le séchage de la cramique ,je suis un artiste céramiste professionnel .
Bon article de vulgarisation de l’intérêt a adopter cette technologie par les céramistes cherchant a faire des économies sur la facture énergétique qui avoisine plus que les 50% du coût de la production